What is LTL Freight Shipping?
What is LTL is a question frequently asked. First, let’s break down the acronym. LTL stands for less than truckload shipping and means exactly that. You are shipping freight, called ltl freight in this case, that does not take up a lot of room. In the most obvious terms, it is the process of shipping freight that does not occupy the whole space of a truck, but rather less than the whole space of a truck or truckload. Less than truckload or LTL freight shipping is used for the transportation of freight that does not require the use of an entire 48 or 53-foot trailer. The typical LTL load is crated or palletized and ranges roughly from 150 to 15,000 pounds. As would be expected, in the past few years, e-commerce companies have have helped LTL freight shipping grow.
What is LTL Freight Shipping?
Less-than-truckload shipping, commonly referred to as LTL, represents a crucial niche within the logistics industry. It’s a specialized mode of transportation that bridges the gap between handling individual parcels and dealing with full truckloads of cargo. In essence, LTL carriers are experts at efficiently moving freight that falls within a specific weight range, typically below approximately 150 pounds (68 kg). Unlike parcel carriers, who focus on small packages, LTL carriers excel at managing larger shipments that can be broken down into manageable units. This unique approach to shipping is a testament to the adaptability and diversity of the modern supply chain, offering a cost-effective solution for businesses with mid-sized freight needs.
We are now in a different supply chain environment than we used to be a long time ago–one that deals mostly with e-commerce and LTL freight shipping.
With LTL, companies can put together their smaller loads and then ship them with other companies’. In doing so, LTL allows businesses to ship freight much more economically. Cost for LTL freight shipping is determined by trailer space used, class of items being shipped, as well as pickup and destination locations.
LTL Freight Shipping is sometimes referred to as the “middle mile” in the whole of the logistics industry.
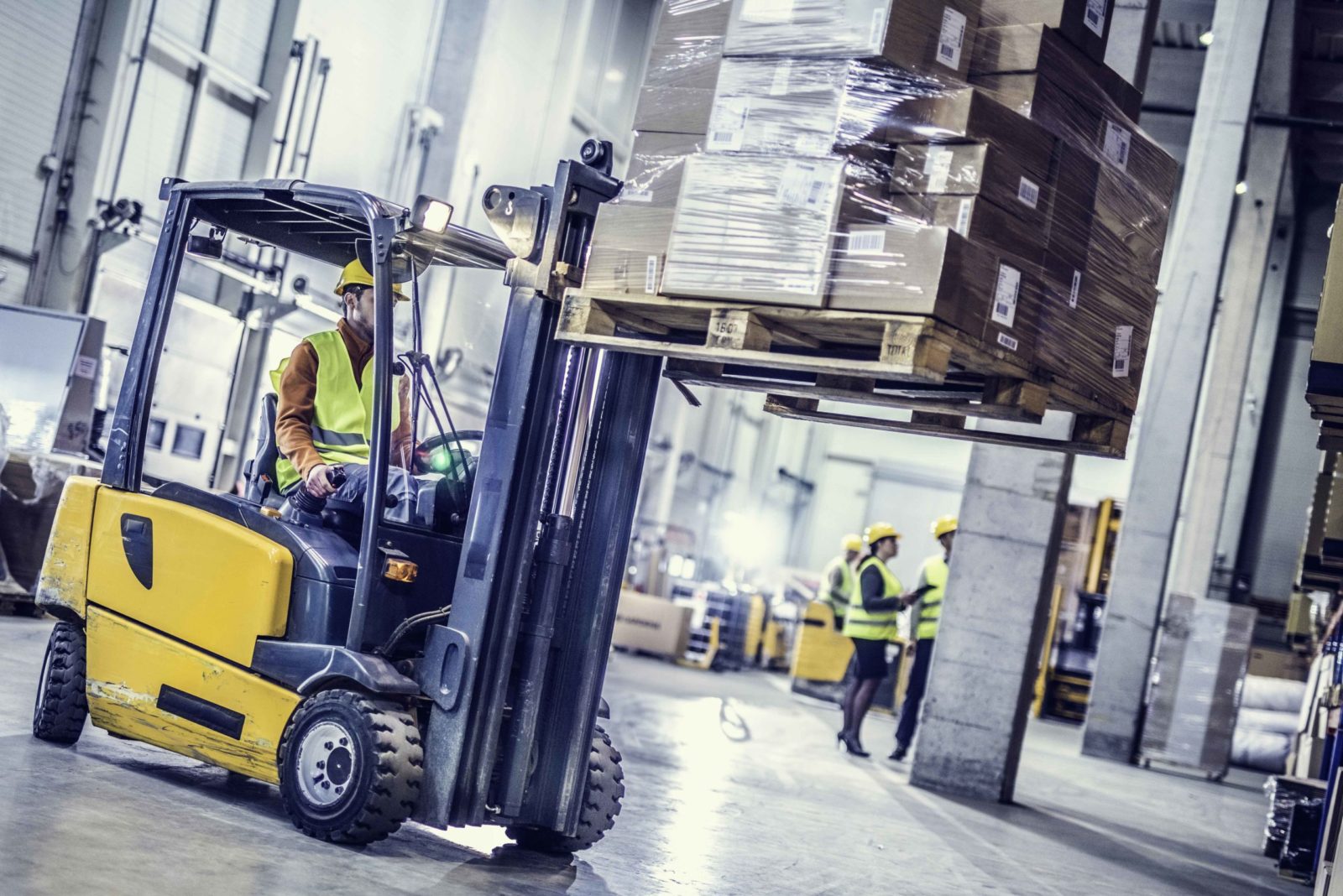
When to Choose LTL
Now that the question as to what is LTL is answered, it’s important to move on to when to choose this type of shipping. The most significant factor in choosing LTL or TL is the weight of the shipment. If your freight tops 10,000 pounds, you will more than likely have to opt for a full truckload. However, if you are under that particular weight, LTL can work. If you are significantly under that weight and are only shipping something small, there is no question that LTL is the way to go. It’s, on average, more bang for your buck, and your shipments are more accessible to track. Another bonus to LTL shipping is that if you have exceptions with your shipment (if your freight was very fragile, for example), they are easier to work around.
LTL Freight Shipping Advantages
Reduces Costs
Since LTL is based on smaller loads from multiple businesses, it reduces the overall shipping cost for everyone. Because your shipment is not using the entire trailer space, you only pay for the space your freight is using.
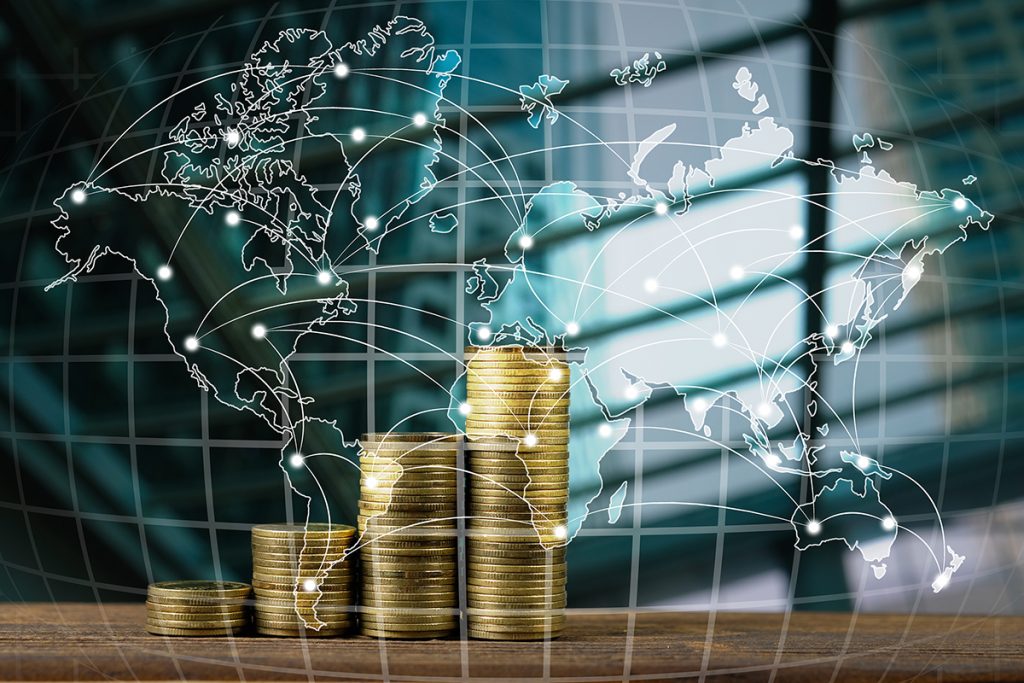
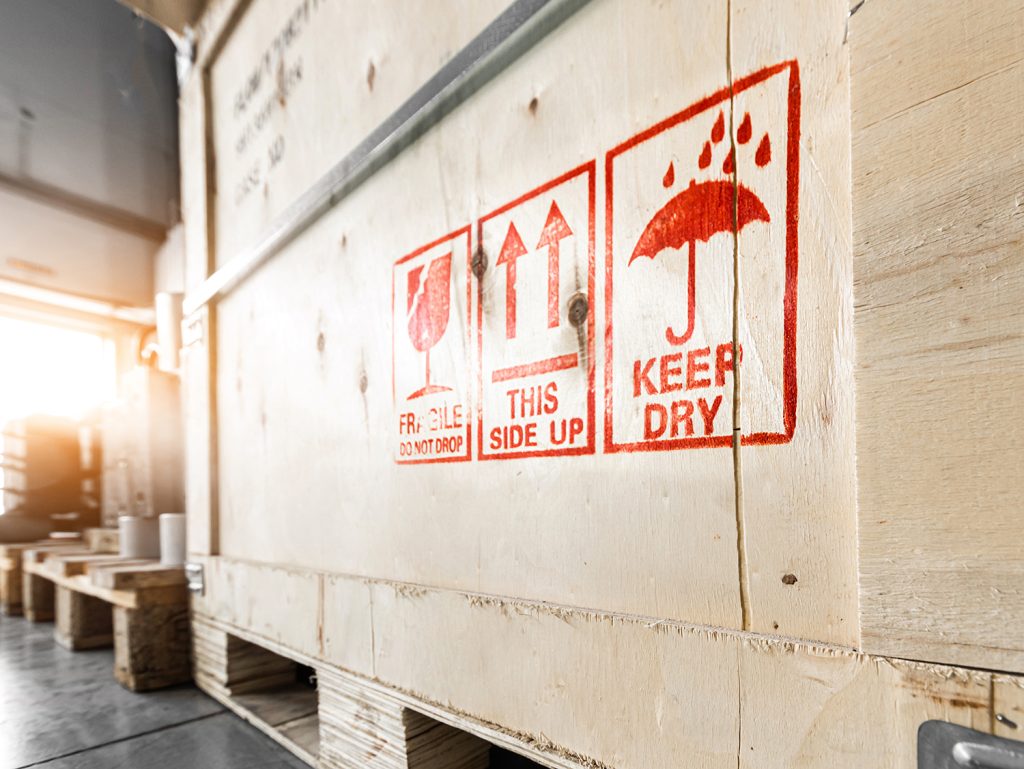
More Service Options
When LTL freight shipping, you gain access to special services that may not be available with other shipping methods. Options include lift gate, expedited shipping, inside pick-up and delivery, freeze protection, special handling, and more. These services do increase cost, but they can also be essential for your shipping needs.
Increases Safety
The first way LTL Freight increases the safety of your shipment is with ample packing performed by the carrier. Packages loaded onto pallets or into crates have a better chance of remaining secure compared to that of small package shipping. Furthermore, LTL Freight carriers usually organize shipping routes with as few stops as possible. This allows them to keep packages safe for the entirety of the trip.
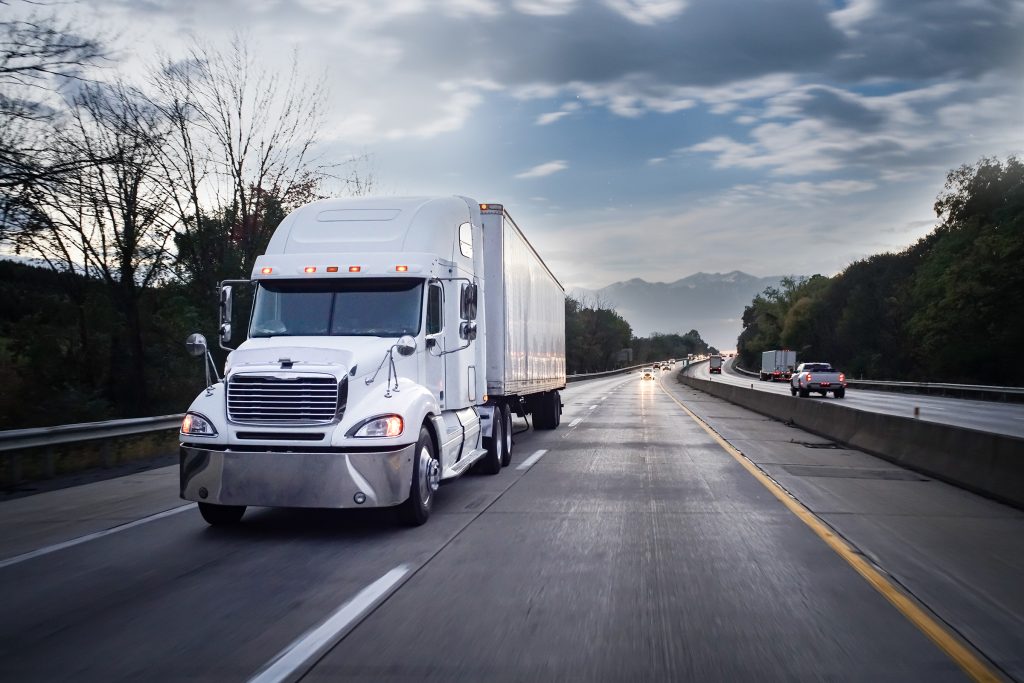
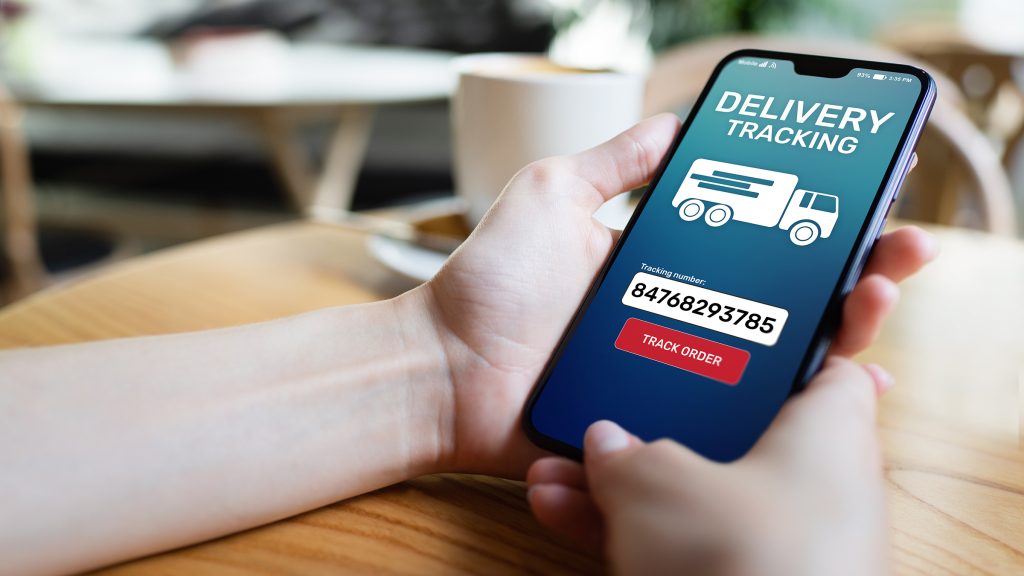
Easier to Track
Many LTL carriers provide real time tracking such as in-transit shipment updates for pick-ups, stop-offs, on time or delayed status, and deliveries. Shipments are tracked by the use of bill of lading number, pro number, PO number, shipment reference number, or pick-up date range.
Environmentally Conscious
Since LTL freight shipping combines shipments from several businesses on one trailer, this results in fewer trucks on the road compared to more trucks at half capacity. Less trucks on the road equals less carbon emissions. Companies now reduce their carbon footprint by utilizing fewer vehicles for shipping.
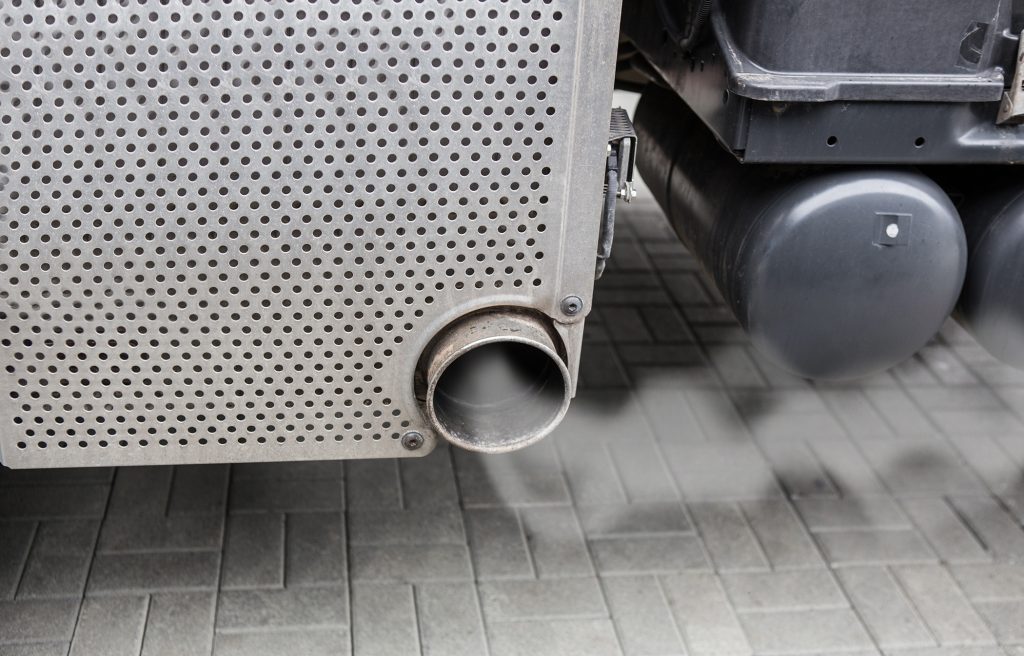
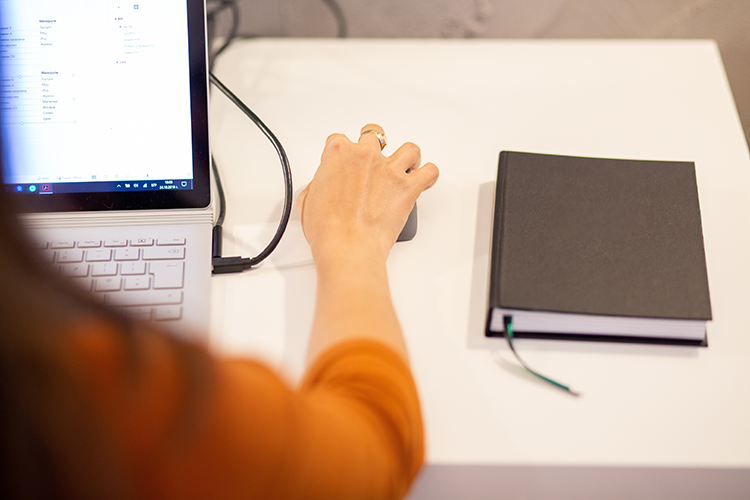
User-Friendly Technology
With today’s technology advancements, cloud-based transportation management systems (TMS) make it easier than ever for businesses to process their LTL shipments. A TMS allows organizations to view rates from multiple carriers, book loads online, track orders and receive business intelligence.
LTL Freight Shipping Disadvantages
Dings and Dents During the Transit Process
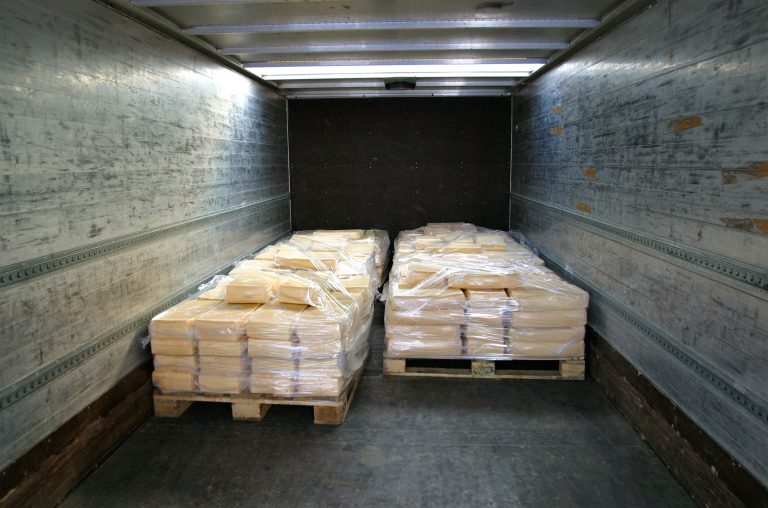
One of the challenges of LTL shipping is that freight often gets transferred and jostled between different trucks at LTL hubs. This movement inevitably increases the chances that damages may occur. The number of cargo transfers depend on a few factors like mileage, the final destination, the arrangement of goods, etc., so it’s difficult to predict the exact number of times that freight could get damaged.
No Assurance of an Exact Delivery Date
It’s tough to pinpoint an exact date and time for freight delivery with LTL shipping. If that is crucial to the shipment, it can be configured but will most likely be an extra fee associated.
Increasing Prices
While LTL is typically cheaper than Full Truckload Shipping, prices have been on the rise recently.
Connectedness
You can ship to areas that are farther out of scope in terms of location than the carrier usually delivers. If this happens, you need to connect with freight forwarders to get your freight to its final destination. It’s an extra step in the shipping process
Common Questions About LTL Freight Shipping
What is the Difference Between LTL and FTL?
Freight that does not require the entire space of a trailer is known as LTL shipping, whereas full truckload shipments fill the space or meet the weight limit.
What Type of Freight is Best Suited for LTL?
LTL is ideal when freight doesn’t require the use of an entire trailer and weighs between 150 and 15,000 pounds.
How Does LTL Reduce Freight Shipping Costs?
When booking an LTL shipment, you only pay for the portion of the trailer used. The rest of the cost is covered by the other occupants of the trailer’s space.
- Distance: Typically the longer the haul, the higher the price
- Mode: Expedited or refrigerated shipments can incur higher prices
- Dimensions: The dimensions and weight of the shipment help determine the freight class, which directly impacts rates
- Type: Special handling (lift-gates, inside delivery) or commodity (perishables, fragile, hazardous items) will lead to higher costs.Type: Special handling (lift-gates, inside delivery) or commodity (perishables, fragile, hazardous items) will lead to higher costs.
How are LTL Shipments Tracked?
LTL carriers offer tracking capabilities through the bill of lading number, PRO number, PO number, shipment reference number and pick up date range, to name a few.
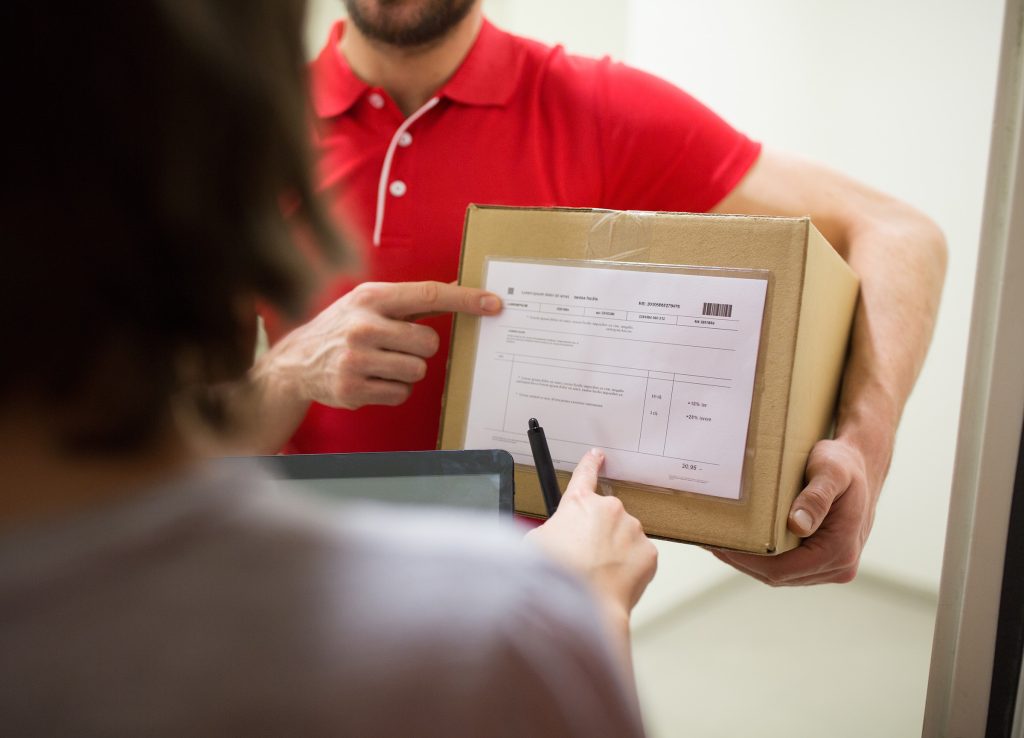
How are Shipping Rates Determined?
Determining shipping rates can be a tricky business because it is very involved. For the most part, these prices are based on the NMFC system but are subject to fluctuations within the market at any given time. Regardless of what you may be shipping, the below criteria play a massive role in figuring out what the rate will be:
- Mode of transportation
- Shipment dimensions
- Weight
- Origin and final destination SeasonalityWeight Origin and final destination
- Seasonality
What is an NMFC Number?
NMFC is the National Motor Freight Classification. People interchange LTL Freight Class and NMFC Codes), but they are different. Freight class is the category of items, while NMFC codes are the individual commodity. The codes break down freight classes one step further to streamline freight categorization and pricing across the industry.
For example, computers and refrigerators may be the same 92.5 freight class, but the respective NMFC codes are 5700 and 6500.
NMFC codes and classifications combine four distinct factors: density, handling, stowability, and liability.
Density
You determine an item’s density by its weight and dimensions, so the higher the density of a shipment, the lower the class, and ultimately, the lower the cost for shipping. This calculation may seem backward at first glance, but consider this: carriers love compact but heavy shipments. A shipment with a higher density means they can fit more products in one load and increase their revenue for the transport.
Liability
Liability considers the probability of your shipment getting damaged, stolen, causing damage to other items, the shipment perishing, or potential theft.
Handling
Handling is the item’s ability to be handled as the freight is loaded and unloaded from one LTL terminal to the next LTL terminal. Dimensions, fragility, and packaging all play a role in how difficult an item is to handle.
Stowability
Stowability means how carriers can arrange your shipment with other shipments in one load. Take into account hazardous shipments (which cannot travel with non-hazardous shipments) or shipments with odd dimensions that limit the amount of freight loaded around them.
What is a Bill of Lading?
As discussed, a bill of lading (BOL) is documentation that involves every detail needed for the expedition of a shipment. A BOL serves as a legally binding contract between the carrier and shipper, among other things. It is a “must” if you are preparing to ship anything LTL. It’s best practice to have the form filled out to completion beforehand.
What are Accessorial fees?
Accessorial fees are extra charges a customer incurs that exceed standard shipping charges. For example, an order may require a liftgate if a school orders desks and chairs but doesn’t have a dock for unloading. Liftgates go beyond standard delivery procedures, so it would be considered an accessorial charge. Other standard accessorial charges include oversized items, frequent stop-offs, residential deliveries, and storage.
How Long Does it Take to Ship Freight?
There is no one answer to this question. The shipping time frame depends on the final destination, speed of transfers, and anything exceptional about the particular commodity.
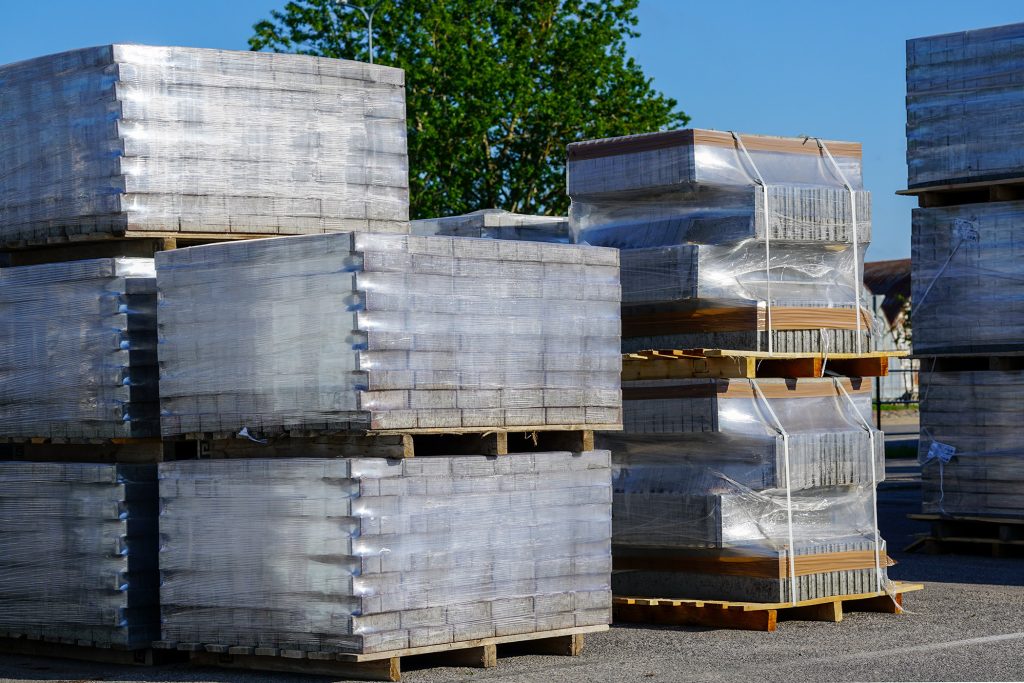
What’s the Best Way to Package Products?
Selecting your packaging depends on what you are shipping. There are multiple modes of shipping, including crates, boxes, pallets, and beyond, but it solely depends on the actual commodity. When making your selection, ask crucial questions like does it need to be in a temperature-controlled setting, etc., to minimize any damage through the shipping process.
What Carrier Should I Choose?
Choosing a carrier that best fits your business’s needs is vital to the entirety of the shipping process. To guarantee on-time freight delivery, you must do your research. On the whole, choose a company who specializes in LTL freight shipping and has a stellar reputation.
Factors on Shipping Rates
1. Density
In LTL freight services, density is the space a shipment occupies relating to its weight. You can find your shipment’s density by dividing the item’s weight in pounds by the volume in cubic feet.
2. Weight
The more your shipment weighs, the less you will pay in LTL freight rates per hundred pounds. The freight rates classify shipments into weight groups, so be aware if your load is approaching the lowest weight of the next highest group.
3. Distance
In general, a long haul means a higher price per hundredweight. Be aware of whether your LTL carrier only serves specific zip codes. If your destination is outside of their service zone, they may transfer the shipment to another carrier, resulting in a higher cost for you.
4. Base Rates
Each LTL carrier establishes its own LTL base rates, which they quote per 100 pounds, or CWT. The CWT calculation is, in turn, based on the volume, gross cost, and freight classification.
5. Freight Classification
The freight class is a significant factor in determining LTL freight rates. The National Motor Freight Classification system determines each shipment’s freight class. The system has 18 classes from 50 to 500 and uses product density, stowability, value, handling, and liability to classify shipments.
6. Minimums
A carrier won’t charge below the cost of its absolute minimum charge (AMC). In general, minimums at LTL carriers are increasing, as the costs a carrier faces for a minimum charge shipment overtakes the costs for heavier loads.
7. Accessorials/Surcharges
These charges come from LTL freight companies’ extra services beyond the standard dock-to-dock pickup and delivery. The most common accessorial cost is a fuel surcharge, but other standard charges include lift gate service, residential pickup or delivery, and limited access location delivery.
Preparing LTL Shipments
Dimensions and Sizing
To ensure that your LTL shipments don’t incur extra costs, make sure to take ample time to measure the exact size of your shipment, always rounding up to the next inch. Although it may not seem vital, inaccurate dimensions can make a substantial difference in the amount owed for a shipment.
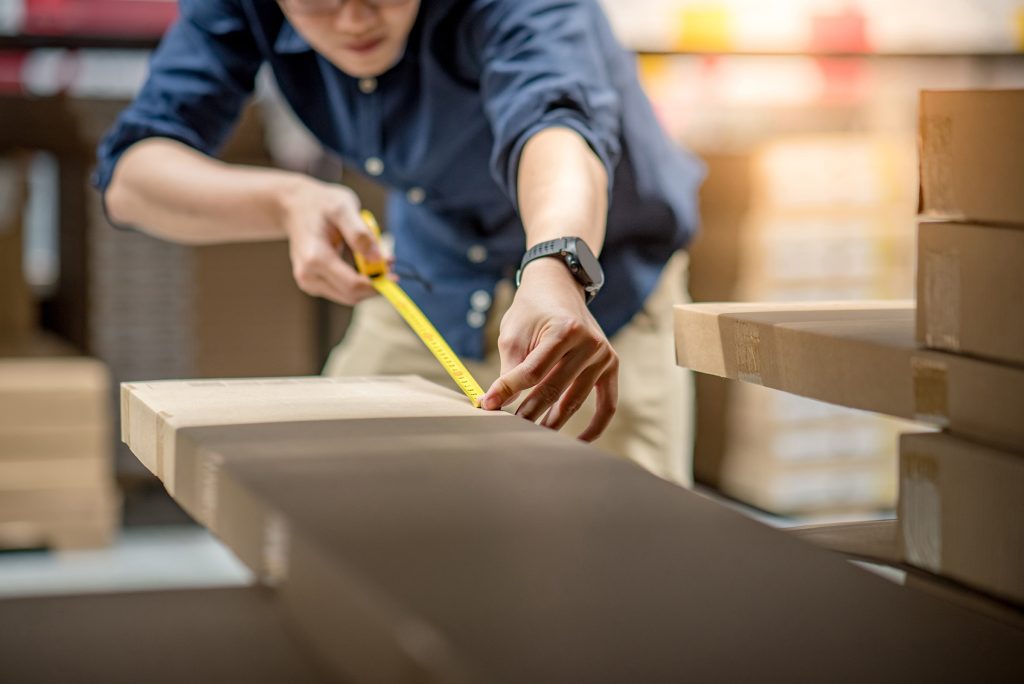
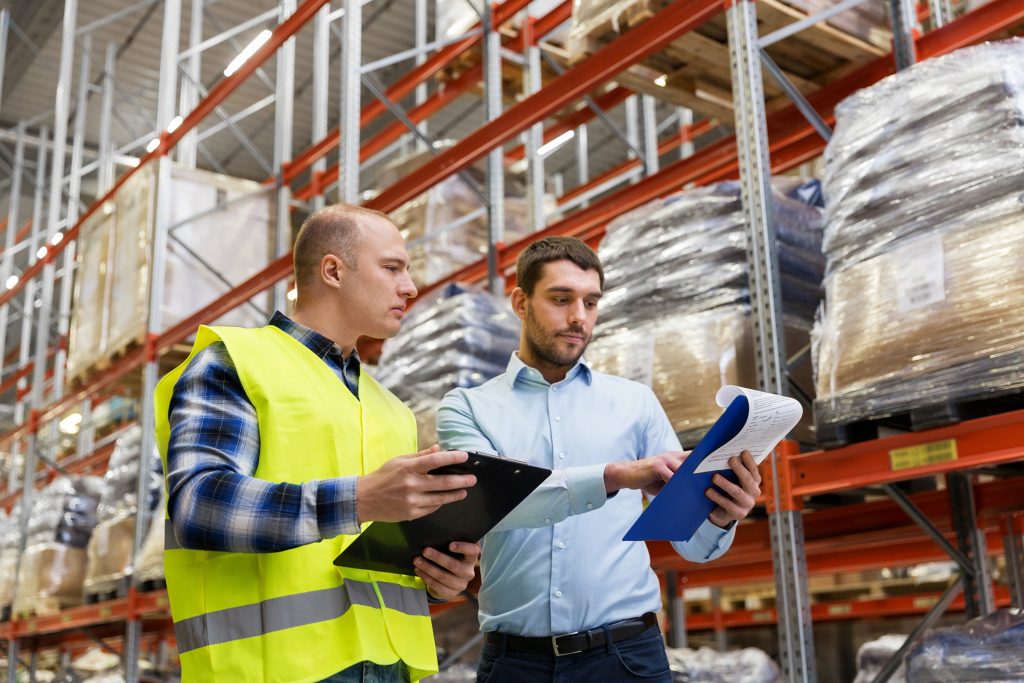
Documentation for LTL Shipping
To prepare for an LTL shipment, ensure that your bill of lading (BOL) is complete. When a carrier arrives to pick up an LTL shipment, they will request this document and assume that all information is accurate. Information needed on the form includes freight class, dimensions (as mentioned above), the final destination, the type of packaging, and so forth.
LTL Packaging and Labeling
Always remember that when loading goods onto pallets, it is best practice to put whatever is heaviest on the bottom of the stack and what is lighter towards the top. Correct packaging will make the LTL process smoother as a whole. Also, each pallet, crate, or container should have a designated label so that anyone involved in the LTL shipping process can know what is within the shipment.
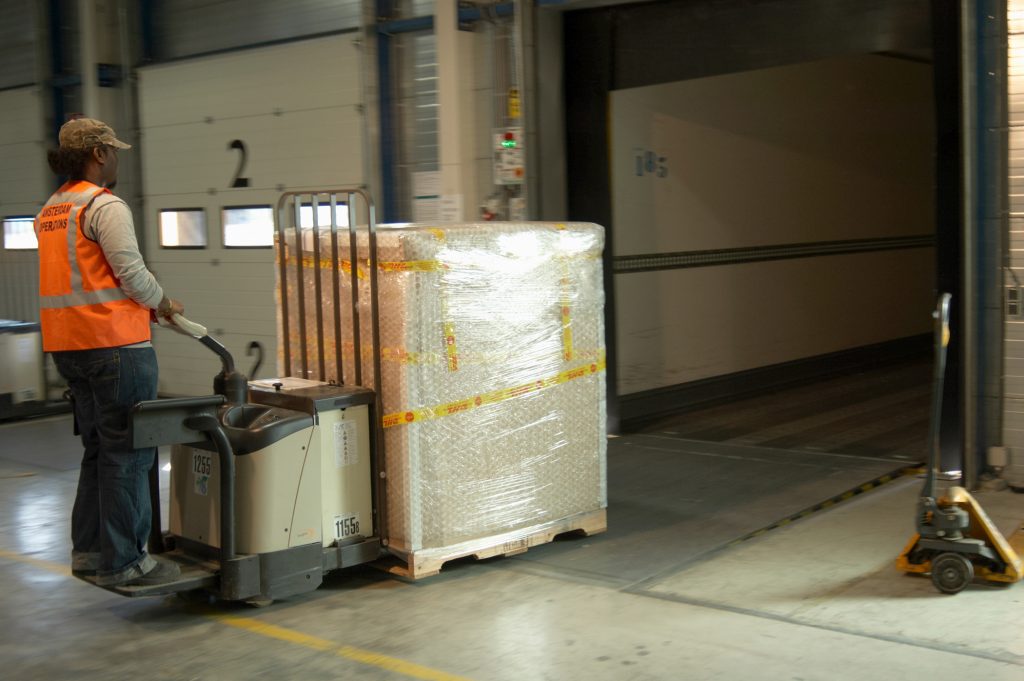
What’s the Difference Between Less Than Truckload (LTL) and Truckload Shipping?
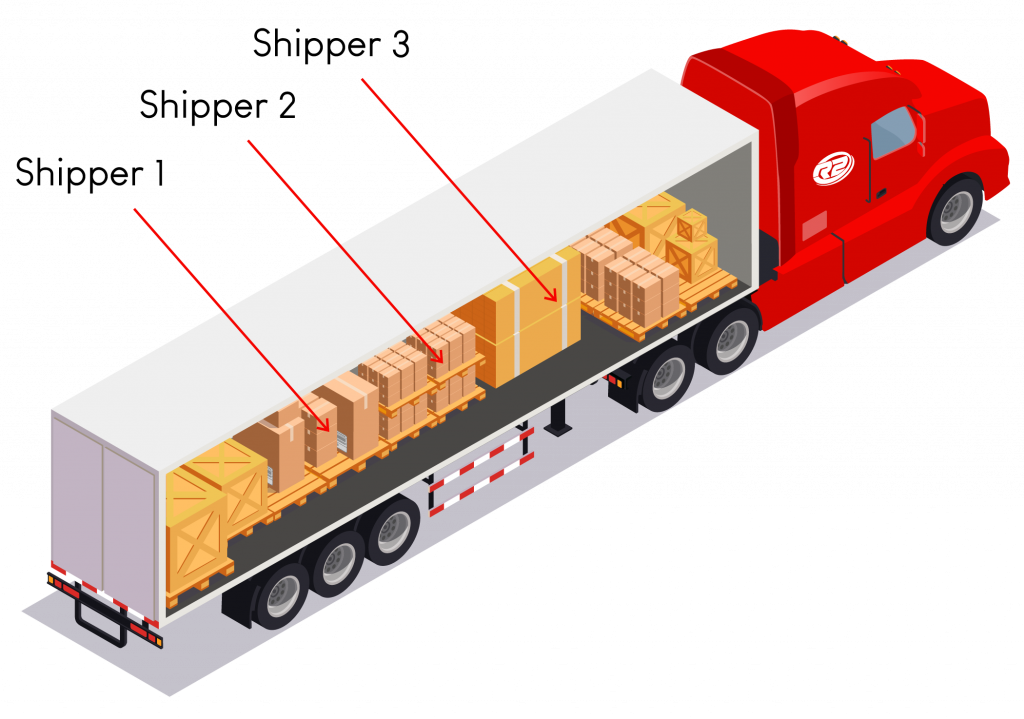
Less Than Truckload (LTL)
A less than truckload (LTL) trailer is filled up with pallets from individual shippers who are paying for space based on the dimensional space of their goods.
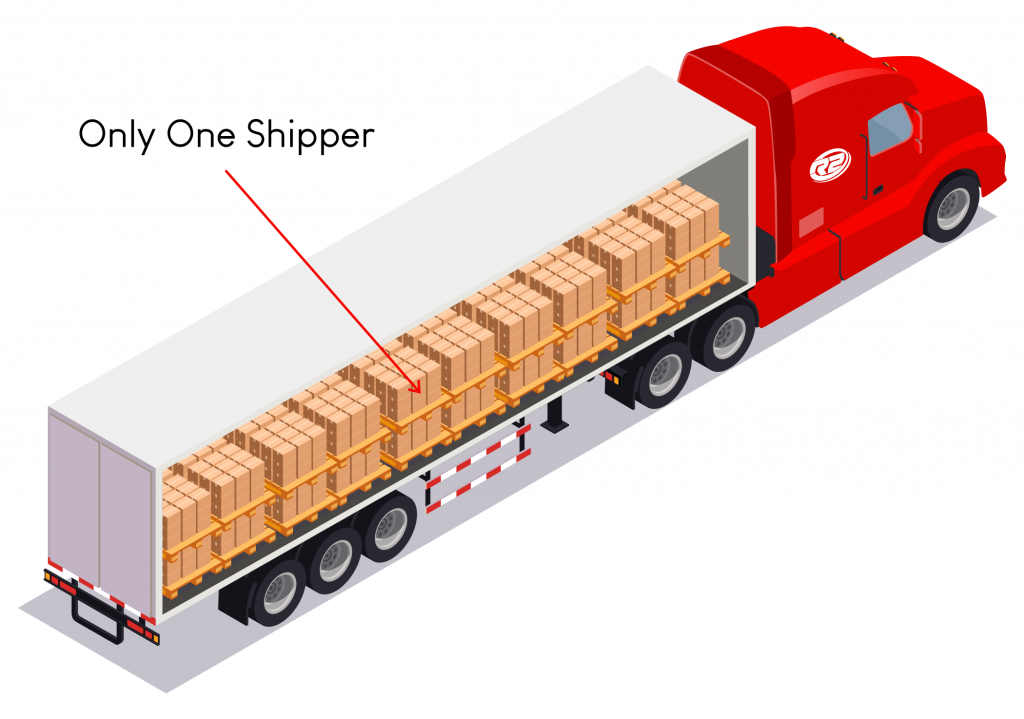
Truckload (TL)
The entire trailer is filled with goods from the same shipper. Truckload shipping offer cost savings when you have a full trailer to ship and maximize space available in the full trailer.
LTL Case Study #1
Auto Company
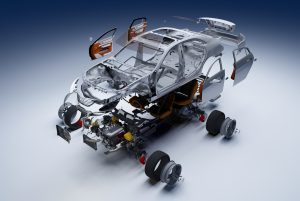
-
Problem
An auto company supplier had multiple time-sensitive LTL shipments that needed to be delivered every week. Coordination and timing were key factors in ensuring success. With their previous transportation provider, on-time pickup and delivery were hit or miss and causing a strain on customer relations and turning a somewhat complicated process into a very overwhelming process.
-
Solution
With the R2 TMS, the supplier is now able to select from multiple LTL carriers that include delivery guarantees. The supplier has options and the options specifics are transparent. In addition, R2’s TMS tracking capabilities increased visibility throughout the delivery process so the supplier had more of an inside perspective into where the shipments were located in the process.
-
Value Added
The supplier and customer have both benefitted from a reliable delivery schedule. The customer no longer has to slow down production to wait for missing parts, and their confidence in the supplier has increased business orders. It’s a win-win for all involved and their bottom line and efficiency has increased.
-
Problem
An R2 Logistics customer in the food and beverage industry brought in new business into their portfolio through a merger and acquisition. This brought on new challenges from the acquired company’s pre-existing and antiquated supply chain processes. They need systems and processes to be streamlined.
-
Solution
The customer integrated with R2’s Transportation Management System. In doing so, they were able to develop logistics solutions seamlessly for their acquired business and gained new visibility across their existing and new supply chain. Everyone was on the same page and the TMS really enhanced the already existing processes.
-
Value Added
With higher visibility and added reporting features, the customer has seen 14% cost reductions in transportation spend — something directly attributed to a 3PL that puts the clients’ needs first.
Case Study #2
Food and Beverage
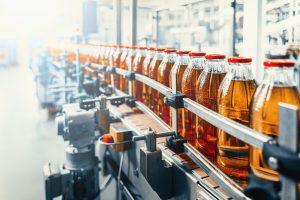
LTL Case Study #3
Retail and Consumer
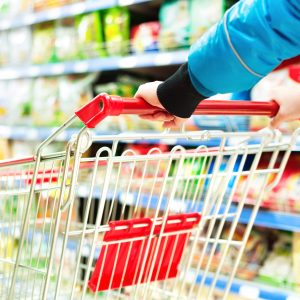
-
Problem
A manufacturer in the retail and consumer space transported their merchandise with a regional LTL carrier. Due to their growing business, their brand was now going to be sold nationally and they needed more shipping options beyond their previous provider. They needed to expand as they had outgrown their original shipping methods.
-
Solution
The manufacturer started using the R2 TMS and was introduced to, and given access to, several nationwide carriers with competitive pricing. They had a wide selection of who to work with, based on their LTL freight abilities. They also found and utilized additional LTL carriers capable of servicing the region handled by their previous carrier.
-
Value Added
The manufacturer was able to roll out their merchandise nationwide and continue their growth strategy without issue. With the ability to compare prices between multiple LTL carriers, they also found significant cost savings across their supply chain. R2 helped them grow and helped them save—two benefits of working with a 3PL.
LTL Case Study #1
Auto Company
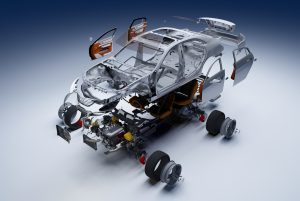
-
Problem
An auto company supplier had multiple time-sensitive LTL shipments that needed to be delivered every week. Coordination and timing were key factors in ensuring success. With their previous transportation provider, on-time pickup and delivery were hit or miss and causing a strain on customer relations and turning a somewhat complicated process into a very overwhelming process.
-
Solution
With the R2 TMS, the supplier is now able to select from multiple LTL carriers that include delivery guarantees. The supplier has options and the options specifics are transparent. In addition, R2’s TMS tracking capabilities increased visibility throughout the delivery process so the supplier had more of an inside perspective into where the shipments were located in the process.
-
Value Added
The supplier and customer have both benefitted from a reliable delivery schedule. The customer no longer has to slow down production to wait for missing parts, and their confidence in the supplier has increased business orders. It’s a win-win for all involved and their bottom line and efficiency has increased.
-
Problem
An R2 Logistics customer in the food and beverage industry brought in new business into their portfolio through a merger and acquisition. This brought on new challenges from the acquired company’s pre-existing and antiquated supply chain processes. They need systems and processes to be streamlined.
-
Solution
The customer integrated with R2’s Transportation Management System. In doing so, they were able to develop logistics solutions seamlessly for their acquired business and gained new visibility across their existing and new supply chain. Everyone was on the same page and the TMS really enhanced the already existing processes.
-
Value Added
With higher visibility and added reporting features, the customer has seen 14% cost reductions in transportation spend — something directly attributed to a 3PL that puts the clients’ needs first.
Case Study #2
Food and Beverage
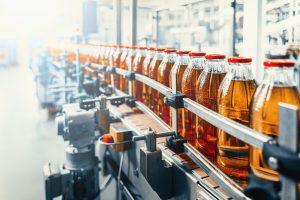
LTL Case Study #3
Retail and Consumer
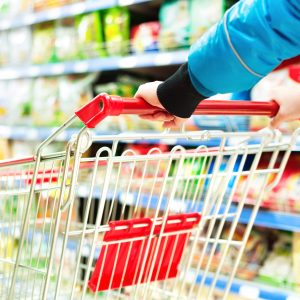
-
Problem
A manufacturer in the retail and consumer space transported their merchandise with a regional LTL carrier. Due to their growing business, their brand was now going to be sold nationally and they needed more shipping options beyond their previous provider. They needed to expand as they had outgrown their original shipping methods.
-
Solution
The manufacturer started using the R2 TMS and was introduced to, and given access to, several nationwide carriers with competitive pricing. They had a wide selection of who to work with, based on their LTL freight abilities. They also found and utilized additional LTL carriers capable of servicing the region handled by their previous carrier.
-
Value Added
The manufacturer was able to roll out their merchandise nationwide and continue their growth strategy without issue. With the ability to compare prices between multiple LTL carriers, they also found significant cost savings across their supply chain. R2 helped them grow and helped them save—two benefits of working with a 3PL.