LTL Case Study #1
Auto Company
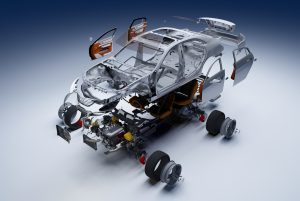
-
Problem
An auto company supplier had multiple time-sensitive LTL shipments that needed to be delivered every week. Coordination and timing were key factors in ensuring success. With their previous transportation provider, on-time pickup and delivery were hit or miss and causing a strain on customer relations and turning a somewhat complicated process into a very overwhelming process.
-
Solution
With the R2 TMS, the supplier is now able to select from multiple LTL carriers that include delivery guarantees. The supplier has options and the options specifics are transparent. In addition, R2’s TMS tracking capabilities increased visibility throughout the delivery process so the supplier had more of an inside perspective into where the shipments were located in the process.
-
Value Added
The supplier and customer have both benefitted from a reliable delivery schedule. The customer no longer has to slow down production to wait for missing parts, and their confidence in the supplier has increased business orders. It’s a win-win for all involved and their bottom line and efficiency has increased.